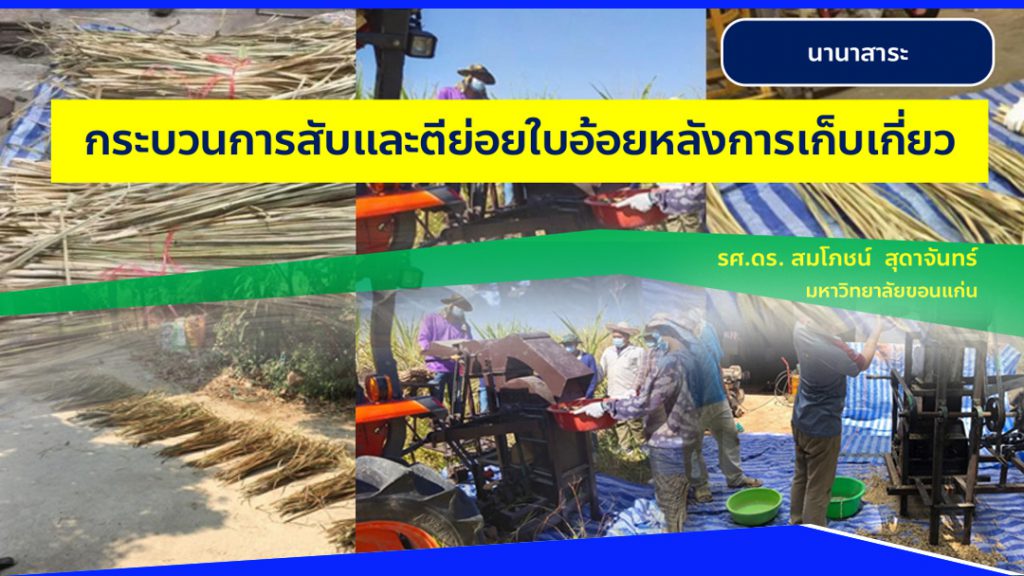
โดย รศ.ดร. สมโภชน์ สุดาจันทร์ มหาวิทยาลัยขอนแก่น
ประเทศไทยมีพื้นที่เพาะปลูกประมาณ 12.10 ล้านไร่ หลังจากการเก็บเกี่ยวอ้อยจะมีใบอ้อยที่เหลือทิ้งไว้ในไร่ประมาณ 17.0 ล้านตัน สามารถนำมาผลิตเป็นพลังงานไฟฟ้าได้ถึง 1,647 เมกะวัตต์ (กรมพัฒนาพลังงานทดแทนและอนุรักษ์พลังงาน, 2563) ปริมาณอ้อยเข้าหีบจากโรงงานน้ำตาลทั่วประเทศ มีอ้อยสดที่เข้าหีบประมาณ 50.94 ล้านตัน และอ้อยไฟไหม้ 80.03 ล้านตัน รวมปริมาณอ้อยที่เข้าหีบทั้งสิ้น 130.97 ล้านตัน (สำนักงานคณะกรรมการอ้อยและน้ำตาลทราย, 2562) แสดงให้เห็นว่าเกษตรกรส่วนใหญ่นิยมเผาอ้อยก่อนเก็บเกี่ยว หากเกษตรกรหรือผู้ประกอบการนำใบอ้อยมาเป็นวัสดุเชื้อเพลิงร่วมกับวัสดุเกษตรอื่นขายให้โรงไฟฟ้าชีวมวลหรือโรงงานน้ำตาล จะช่วยลดการเผาอ้อยและเพิ่มคุณภาพความหวานของน้ำตาล โดยราคาซื้อขายใบอ้อยในปัจจุบันอยู่ที่ประมาณ 1,000 บาทต่อตัน แต่ใบอ้อยมีความหนาแน่นต่ำ ความชื้นแตกต่างกัน การจัดการเก็บและการขนส่งที่ยุ่งยาก การนำวัสดุมาขึ้นรูปโดยการอัดเป็นเม็ดหรือแท่ง ผลิตเป็นเชื้อเพลิงอัดเม็ดจะเพิ่มมูลค่าถึง 3,000-3,500 บาทต่อตัน เพิ่มความหนาแน่นและลดความชื้นของวัสดุ ช่วยให้ง่ายต่อการควบคุมปริมาณน้ำหนัก และขนาดให้มีความสม่ำเสมอ (กระทรวงวิทยาศาสตร์และเทคโนโลยี, 2561) การลดขนาดอนุภาคในการเตรียมวัสดุให้พร้อมสำหรับนำไปใช้ในการแปรรูป ถือว่าเป็นขั้นตอนสำคัญ ประกอบไปด้วย 2 ขั้นตอน ได้แก่ การสับให้วัสดุมีขนาดเล็กลงประมาณหนึ่งก่อนด้วยเครื่องสับจากนั้น ขั้นตอนต่อไปนำไปตีย่อยให้ละเอียดด้วยเครื่องตีย่อย เพื่อเพิ่มพื้นที่ผิวสัมผัสกันระหว่างอนุภาคลดแรงเสียดทานของอัตราการไหลของวัสดุ (Jezerska et al., 2016) ขนาดอนุภาคของวัสดุจึงเป็นเกณฑ์กำหนดความเหมาะสมสำหรับนำไปแปรรูปอัดเม็ด โดยวัสดุควรมีขนาดอนุภาคสม่ำเสมอน้อยกว่า 3.2 มิลลิเมตร (Mani et al., 2006) หรือ มีค่าเฉลี่ยทางเรขาคณิตของขนาดอนุภาคน้อยกว่า 0.640 มิลลิเมตร (Mani et al., 2004) ซึ่งเมื่อต้องการอนุภาคที่มีขนาดเล็กจะใช้พลังงานสูง และเวลาค่อนข้างนาน ซึ่งกระบวนการสับ และการตีย่อยมีการแยกระบบการทำงาน ทำให้ไม่มีความต่อเนื่องในการทำงาน ต้องขนย้ายวัสดุจากเครื่องหนึ่งไปยังอีกเครื่อง เป็นการเพิ่มเวลาในการทำงานมากขึ้น การพัฒนากระบวนการสับและตีย่อยให้สามารถใช้งานได้ในระบบเดียวกัน และขนาดอนุภาคที่ได้หลังการสับย่อยมีขนาดที่เหมาะสมต่อการนำไปใช้งานจึงมีความสำคัญ สำหรับเป็นแนวทางในการนำเศษวัสดุเหลือใช้มาใช้ให้เกิดประโยชน์ เพื่อเพิ่มปริมาณเชื้อเพลิงในการผลิตพลังงานไฟฟ้า ช่วยสร้างงานเพิ่มรายได้ให้แก่เกษตรกร และลดการเผาใบและยอดอ้อยหลังการเก็บเกี่ยว
1. การลดขนาดวัสดุเหลือทิ้งจากไร่อ้อย
วัสดุเหลือทิ้งในไร่อ้อยหลังการเก็บเกี่ยว ได้แก่ ยอดและใบอ้อยมีความหนาแน่นต่ำ และขนาดไม่เหมาะสมต่อการนำมาใช้เป็นเชื้อเพลิง เพราะขนาดของเชื้อเพลิงมีผลกระทบต่ออัตราการระบายความร้อน และความต้องการอากาศเพิ่มขึ้นของหม้อไอน้ำ ฉะนั้นประสิทธิภาพการเผาไหม้ของหม้อไอน้ำจึงขึ้นอยู่กับขนาดของวัสดุเชื้อเพลิง ถ้าวัสดุที่ใช้เผาไหม้มีขนาดที่เหมาะสมแล้ว จะทำให้เกิดการเผาไหม้ที่สมบูรณ์ (วรายุทธ, 2538) จากรายงานการวิจัยของ Jorapur and Rajvanshi (1995) กล่าวว่า ขนาดของใบอ้อยที่เหมาะสมต่อการนำไปเป็นเชื้อเพลิงในการเผาไหม้ควรมีขนาดอยู่ในช่วง 2-10 เซนติเมตร ใบอ้อยเป็นวัสดุชีวมวลที่มีความหนาแน่นต่ำ เมื่อได้รับความร้อนจะเกิดการลุกไหม้อย่างรวดเร็ว การนำวัสดุที่ผ่านการสับย่อยมาอัดเม็ดจะเป็นการเพิ่มความหนาแน่นของวัสดุให้มากขึ้น ทำให้ได้ปริมาณของเชื้อเพลิงเพิ่มขึ้นและสะดวกต่อการนำไปใช้เป็นวัตถุดิบเชื้อเพลิงด้วย
2. หลักการลดขนาด
การลดขนาดวัสดุ คือ การทำให้อนุภาคของวัสดุถูกตัดหรือทำให้มีอนุภาคเล็กลง ซึ่งเป็นไปพร้อมๆ กับการเพิ่มพื้นที่ผิวให้กับกลุ่มก้อนหรือเม็ดวัตถุด้วย การลดขนาดเป็นขั้นตอนแรกๆ ในการขนถ่ายวัสดุชีวมวลและการประยุกต์ใช้งาน การเลือกใช้อุปกรณ์ในการลดขนาดที่เหมาะสมมีความสำคัญมากสำหรับการเตรียมวัสดุชีวมวล ตัวแปรหลักในการเลือกอุปกรณ์ลดขนาดที่เหมาะสม คือ พลังงานที่ต้องใช้ในการลดขนาด (Naimi et al., 2006) การที่ของแข็งคงอยู่เป็นรูปร่างได้เนื่องจากแรงยึดเหนี่ยวระหว่างโมเลกุล ดังนั้น การลดขนาดจึงจำเป็นอย่างยิ่งที่ต้องทำลายหรือเอาชนะแรงยึดเหนี่ยวนี้ด้วยแรงทางกลจากภายนอก วิธีการลดขนาดจะแตกต่างกันขึ้นอยู่กับช่วงของอนุภาคที่ต้องการ ได้แก่ คอมเพลสชัน (Compression หรือ crushing) อิมแพคท์ (Impact หรือ Grinding) แอททริชัน (Attrition หรือ Milling) และการตัด (Cutting)
การสับแบบจานสับ (Disk Chipper) ดังภาพที่ 1 เป็นที่นิยมในอุตสาหกรรมเยื่อกระดาษ การสับแบบจานสับมีใบมีดติดอยู่บนแท่นจานสับที่มีการหมุนเหวียงเพื่อสับวัสดุ ซึ่งจานสับจะหมุนด้วยความเร็วระหว่าง 400-1,000 รอบต่อนาที การสับแบบจานสับสามารถสับไม้ที่มีเส้นผ่านศูนย์กลางตั้งแต่ 350-370 เซนติเมตร กระบวนการสับด้วยจานสับสามารถควบคุมได้โดยการปรับตั้งระดับใบมีด จำนวนใบมีด ความเร็วของจานสับและการป้อนวัสดุ
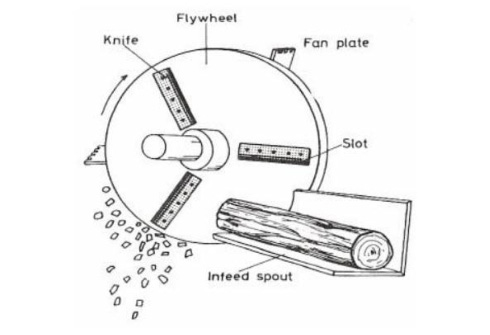
การสับแบบหัวสับทรงกระบอก (Drum Chipper) ดังภาพที่ 2 ซึ่งใบมีดถูกติดตั้งตามแนวรัศมีของชุด หัวสับทรงกระบอก เมื่อเทียบกับการสับแบบจานสับ (Disk Chipper) การสับแบบหัวสับทรงกระบอกมีน้ำหนักมากกว่า แต่การป้อนวัสดุเพื่อสับทำได้ง่ายกว่า การสับแบบนี้สามารถใช้กับวัสดุได้หลากหลายขนาด ขนาดชิ้นวัสดุที่ถูกสับสามารถควบคุมได้โดยใช้ตะแกรงคัดขนาดที่ติดตั้งด้านล่างของชุดสับ
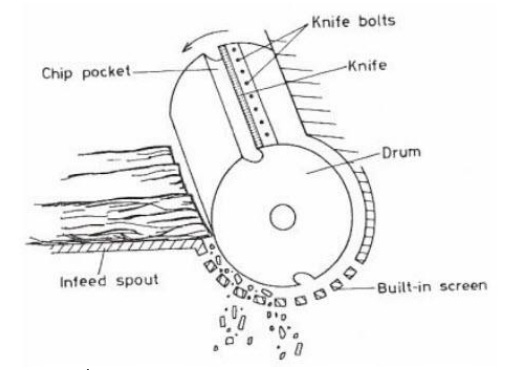
เศษวัสดุบางอย่างมักมีทรายและหินปะปนมาด้วยซึ่งเป็นสาเหตุให้ใบมีดทื่อ จากปัญหาดังกล่าว หลักการลดขนาดวัสดุอีกแบบหนึ่งที่ถูกนำมาใช้ คือ การตีย่อยแบบค้อนตี (Hammer Mill) ดังภาพที่ 3 เป็นการลดขนาดวัสดุด้วยหลักการของการกระแทกด้วยค้อน วัสดุถูกลดขนาดด้วยการอัดตัว ขนาดของวัสดุถูกควบคุมด้วยตะแกรงคัดขนาดที่ติดตั้งอยู่ด้านล่าง
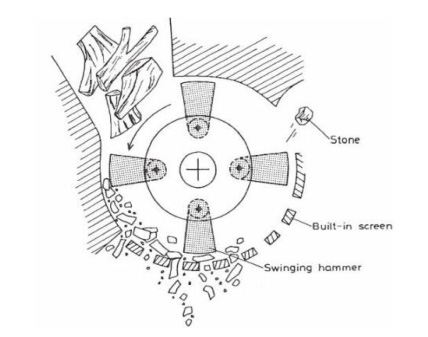
3. การพัฒนาเครื่องสับและตีย่อยใบอ้อย
เครื่องสับย่อยใบอ้อยต้นแบบที่พัฒนาขึ้นมา (ภาพที่ 4) มีส่วนประกอบหลักดังนี้ 1) ถังป้อนหรือถาดรับวัสดุ ทำเป็นกล่องสี่เหลี่ยมคางหมูยื่นออกมา 400 มิลลิเมตร และสามารถปรับมุมได้เพื่อรองรับวัสดุที่ป้อน 2) ลูกกลิ้งป้อนวัสดุตัวบน และตัวล่างสามารถปรับขยายช่องป้อนได้ 3) แท่นรองตัด 4) ชุดหัวสับทรงกระบอก ติดใบมีดสับ 6 ใบ ให้ระยะห่างเท่าๆ กันรอบทรงกระบอก และมุมเอียงใบมีด 10 องศา 5) ช่องทางออกวัสดุหลังสับ 6) ชุดตีย่อย 2 ชุด อยู่ด้านล่างชุดหัวสับ ชุดตีย่อยตัวบนและล่างเป็นแบบ 4 แถว 132 ใบตี หมุนในทิศทางตรงข้ามกัน ขนาดรูตะแกรงบนและล่างมีขนาด 4 และ 3 มิลลิเมตร 7) ฐานยืนป้อนวัสดุ 8) ถาดรองรับวัสดุเพื่อรอป้อน 9) ช่องทางออกวัสดุหลังตีย่อย 10) โครงเครื่องสับพร้อมอุปกรณ์ติดตั้งต่อพ่วงกับต้นกำลังรถแทรกเตอร์ เริ่มทำงานโดยการต่อพ่วงกับ PTO รถแทรกเตอร์ขนาดกำลัง 40 แรงม้า การสตาร์ทเครื่องยนต์ของรถแทรกเตอร์ ปรับคันโยกไปที่เพลาอำนวยกำลัง (PTO) ที่ความเร็วรอบเพลาอำนวยกำลัง 450 รอบต่อนาที ส่งถ่ายกำลังผ่านสายพานไปยังชุดพลูเลย์เพื่อขับเคลื่อนลูกกลิ้งป้อน ชุดหัวสับหมุนด้วยความเร็วรอบ 900 รอบต่อนาที (10.13 เมตรต่อวินาที) และชุดหัวตีย่อยทั้งสองชุดหมุนคนละทิศทางด้วยความเร็วรอบใบตีย่อย 1,100 รอบต่อนาที (26.49 เมตรต่อวินาที) เมื่อเริ่มป้อนลูกกลิ้งป้อนจะหมุนสวนทางกันดึงป้อนวัสดุเข้าสู่ชุดหัวสับ ใบอ้อยจะถูกสับด้วยใบมีดกับแท่นรองตัด ทำให้ใบอ้อยขาดเป็นชิ้นเล็กๆ ไหลเข้าสู่ห้องตีย่อยตัวบน ชุดตีย่อยทำการตีย่อยใบอ้อยจนกระทั้งมีขนาดเล็กกว่ารูตะแกรงแล้วลอดผ่านตะแกรงไปยังห้องตีย่อยตัวล่าง ในขณะที่หัวตีหมุนเหวี่ยงในทิศทางตรงข้ามกับชุดบน ขนาดอนุภาคที่มีเล็กกว่ารูตะแกรงจะลอดผ่านไปยังช่องทางออก
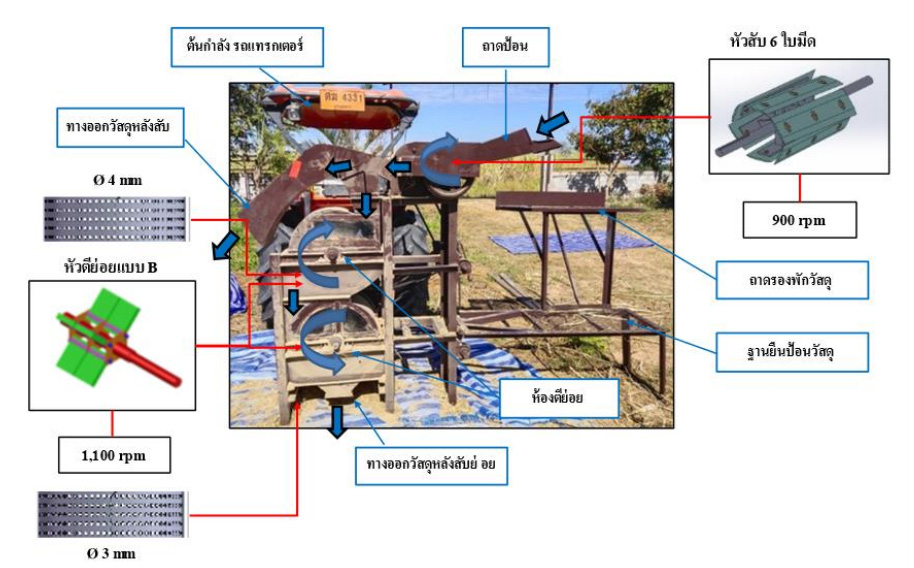
ผลการทดสอบเครื่องสับและตีย่อยใบอ้อย (ภาพที่ 5, 6 และ 7 ตามลำดับ) ในแปลงที่มีความชื้นใบอ้อย 8.23-15.46 เปอร์เซ็นต์มาตรฐานเปียก เครื่องสับและตีย่อยใบอ้อยมีความสามารถในการสับและตีย่อยใบอ้อยเฉลี่ย 29.46-31.43 กิโลกรัมต่อชั่วโมง อัตราการสิ้นเปลืองน้ำมันเชื้อเพลิงเฉลี่ย 2.11-2.22 ลิตรต่อชั่วโมง ขนาดเฉลี่ยของอนุภาค 2.81-2.90 มิลลิเมตร ค่าเฉลี่ยทางเรขาคณิตของขนาดอนุภาคใบอ้อยหลังตีย่อย 0.625-0.639 มิลลิเมตร ความหนาแน่นรวม 91.50-96.09 กิโลกรัมต่อลูกบาศก์เมตร ตามลำดับ ส่วนกรณีทดสอบสับใบอ้อยอย่างเดียว ทดสอบในแปลงที่มีความชื้นใบอ้อย 8.23-52.94 เปอร์เซ็นต์มาตรฐานเปียก มีความสามารถในการสับใบอ้อยเฉลี่ย 87.77-100.51 กิโลกรัมต่อชั่วโมง เปอร์เซ็นต์น้ำหนักที่สับได้ 90.51-96.61 ค่าเฉลี่ยทางเรขาคณิตของขนาดอนุภาคใบอ้อยหลังตีย่อย 6.799-11.046 มิลลิเมตร และอัตราการสิ้นเปลืองน้ำมันเชื้อเพลิงเฉลี่ย 1.54-1.72 ลิตรต่อชั่วโมง
การวิเคราะห์และประเมินผลทางเศรษฐศาสตร์การใช้งานเครื่องสับและตีย่อยใบอ้อย 600 และ 1,080 ชั่วโมงต่อปี ที่ความสามารถในการทำงาน 25 และ 30 กิโลกรัมต่อชั่วโมง มีต้นทุนการทำงานของเครื่องเท่ากับ 7.60, 6.33, 6.99 และ 5.83 บาทต่อกิโลกรัม ตามลำดับ มีระยะเวลาคืนทุนของเครื่องจักรเท่ากับ 2.6 ปี และ 1.3 ปี ตามลำดับ
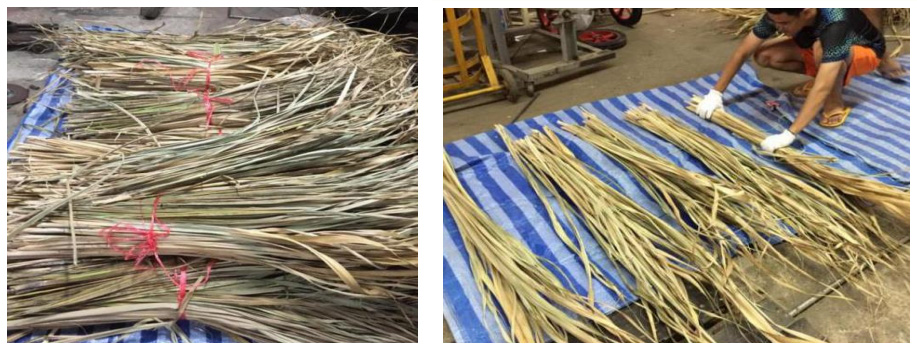
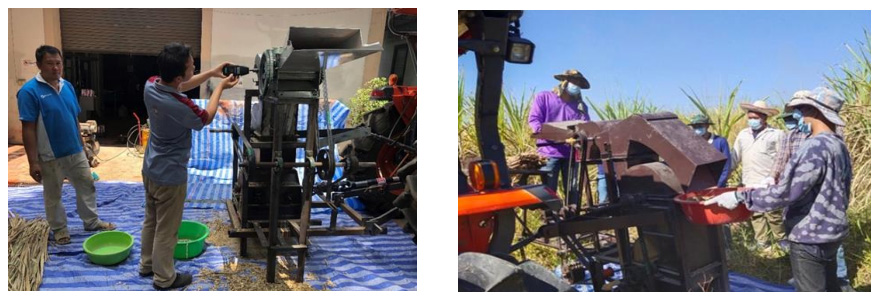
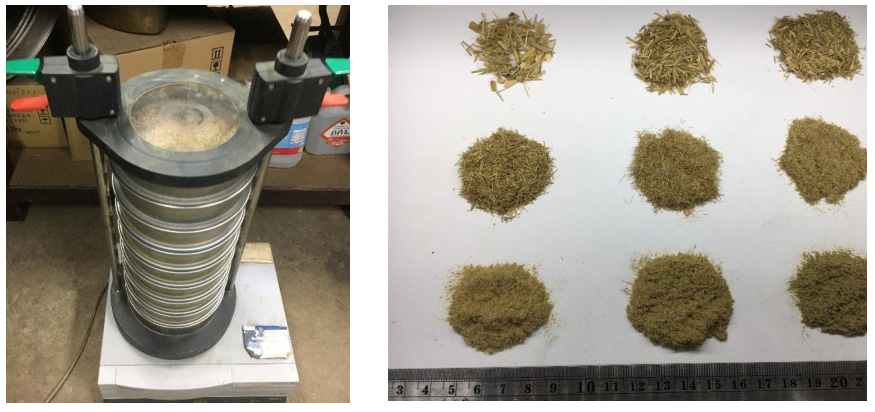
เครื่องสับย่อยใบอ้อยต้นแบบสามารถนำไปสับย่อยใบอ้อยหลังการเก็บเกี่ยวได้ กลุ่มเกษตรกร หรือโรงงานน้ำตาลอาจจะใช้เพื่อช่วยให้สับย่อยใบอ้อยได้ง่ายขึ้น ในขั้นตอนการเตรียมวัสดุสำหรับผลิตเชื้อเพลิง เช่น การลดขนาด โดยการสับหยาบและการตีย่อยละเอียด ก่อนที่จะนำไปผสมกับตัวประสาน และการขึ้นรูปเป็นแท่งหรืออัดเม็ดเชื้อเพลิงในขั้นตอนต่อไป ซึ่งก็จะเป็นการเพิ่มรายได้ให้เกษตรกรผู้ปลูกอ้อย อีกทั้งยังลดมลพิษจากการเผาใบอ้อยก่อนเก็บเกี่ยวด้วย
เอกสารอ้างอิง
- กรมพัฒนาพลังงานทดแทนและอนุรักษ์พลังงาน. 2563. สรุปสถานการณ์พลังงานของประเทศไทย มกราคม-พฤศจิกายน 2563. [ระบบออนไลน์]. แหล่งที่มา: http://www.dede.go.th/download. (12 มีนาคม 2563).
- กระทรวงวิทยาศาสตร์และเทคโนโลยี. 2561. เชื้อเพลิงชีวมวลอัดเม็ด. [ระบบออนไลน์]. แหล่งที่มา: http://www.most.go.th/main/th/165-knowledge/practical-rad/7497-wood-pellet. (10 มกราคม 25562)
- วรายุทธ สุขสวัสดิ์. 2538. ความเป็นไปได้และความเหมาะสมในการใช้ใบและยอดอ้อยเป็นเชื้อเพลิงเสริมในโรงงานน้ำตาล. วิทยานิพนธ์ปริญญาโท. สาขาเทคโนโลยีการจัดการพลังงาน. กรุงเทพฯ : บัณฑิตวิทยาลัยสถาบันเทคโนโลยีพระจอมเกล้าธนบุรี.
- สำนักงานคณะกรรมการอ้อยและน้ำตาลทราย. 2562. รายงานประจำปี 2562. [ระบบออนไลน์]. แหล่งที่มา: http://www.ocsb.go.th. (22 มิถุนายน 2563).
- Jezerska, L., O. Zajonc, J. Vyletelek and J. Zegzulka. 2016. Mechanical material properties effect on palletization. Wood Research 61(2): 307-320.
- Jorapur, R.M. and A.K. Rajvanshi. 1995. Development of a sugarcane leaf gasifier for electricity generation. Biomass and Bioenergy 8 : 91-98.
- Mani, S., L.G. Tabil and S. Sokhansanj. 2004. Mechanical properties of corn stover grind. Trans. ASAE 47(6): 1983-1990.
- Mani, S. L.G. Tabil and S. Sokhansanj. 2006. Grinding performance and physical properties of wheat and barley straws corn stover and switchgrass. Biomass and Bioenergy 27: 339-352.
- Naimi, L.J., S. Sokhansanj, S. Mani, M. Hoque and T. Bi. 2006. Cost and performance of woody biomass size reduction for energy production. In the Canadian Society for Bioengineering. Canada: CSBE/SCGAB, Annual Conference Edmonton Alberta, 16-19 July 2006. p. 1-13.
บทความนี้ตีพิมพ์ลงใน Postharvest Newsletter ปีที่ 20 ฉบับที่ 4 ตุลาคม – ธันวาคม 2564